Eastham company creates Biomass pyrolysis machine to ship to China
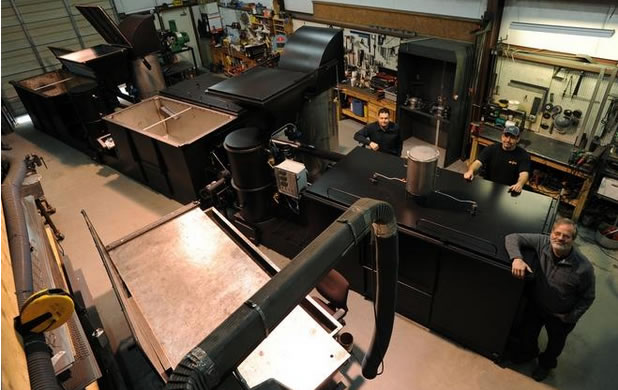
Cape Cod Times
By Lorelei Stevens lstevens@capecodonline.com
EASTHAM – Down a rutted road in a tidy industrial park bay, Bob Wells and his crew are building behemoth machines with the idea of saving the planet.
The devices – each individually designed and handcrafted – are non-polluting, closed systems that transform waste wood into biochar, a charcoal-like soil amendment used to make infertile land rich and keep greenhouse gases out of the environment.
Monday morning, three of New England Biochar LLC’s staff were winding up 13 months of work and preparing to pack up an AR3 Biochar Retort System for shipment to Ocean University of China in Qingdao.
It was a proud moment for the fabricators – Ryan Sverid, shop foreman from Eastham, Chris Thompson of Orleans and Jed Foley of Wellfleet. While some of the pieces were created at local machine shops, the in-house crew shaped, hammered and welded much of the 45-foot-long, 20,000-pound device.
“We come up with our own designs for things that do what we need them to do and we make it ourselves from scratch,” Sverid said. “The waste is minimal. We use scrap pieces to make other things we need.”
Since its founding in 2009, New England Biochar has produced dozens of systems that are in use in Florida, North Carolina and California and has built simpler models onsite in Chile and Indonesia.
“This is the first big one we’ve sent overseas,” Wells said. “It’s essentially three big ovens that will take wood or any biomass and turn it into biochar using every bit of it that we can.”
Wells will spend six weeks in Qingdao helping his clients assemble the unit and training people how to use it.
The process is about as clean and green as it gets. Nearly every component of the system is welded tight and super insulated. The only outside air that gets in is what the operator purposely adds and, even though the temperatures inside the machine typically range from 850 degrees in the biochar retort (similar to a kiln) to 2,000 degrees in the combustion chamber, the outside remains cool to the touch.
Traditional charcoal operations can create huge amounts of potentially polluting smoke, but Wells’ device recycles that smoke to fuel the biochar-making process.
The whole system runs on wood gas, Wells said. The process is kick-started with a downdraft gasifier typically fueled with wood chips that starts heating up the retort. Once the waste wood inside starts heating up, it creates smoke that basically is captured and sorted out.
“It’s a matter of condensing out anything that will condense,” he said. “What doesn’t condense out goes back into the combustion chamber and burns.”
Nothing but water vapor and some carbon dioxide come out of the chimney.
“Our goal is to capture that, too, and pump the CO2 into greenhouses to help plants grow faster,” Wells said.
Besides water and some CO2, the only other byproduct is liquid smoke, which can be sold for use in items such as makeup and food flavorings, Wells said. It can also be diluted and used as a seed-germination accelerator or, in a more concentrated form, as an herbicide. After the liquid smoke byproduct is allowed to settle, the thick tar-like layer at the bottom can be used in asphalt production.
In 2012, Wells started a second company, CharGrow LLC in North Carolina to manufacture biochar – much of it out of waste wood from furniture factories – and package it up for sale to farmers and gardeners.
Biochar is not a fertilizer, Wells explained. Rather, mixing it with other ingredients, such as worm castings, and working it into poor soil changes the soil ecology, allowing it to host important microbes and hold on to nutrients that plants need to grow.
Wells came to biochar organically, you might say.
He and his wife, Connie, settled in a home on a patch of sandy land in Eastham a few-minutes-drive from the Holmes Road industrial park. Over the years, they have beaten back the briars and turned it into Redberry Farm, where they now have several Eastham turnip fields and a large blueberry patch.
“It was the turnips that got me into biochar,” Wells said, pulling up a few of the tubers to reveal the dark, rich earth. “It builds up the soil.”
There’s also a man-made pond on the farm where Wells grows a few fish and does research to document how biochar removes excess nutrients from the water.
Sending a unique piece of potentially revolutionary equipment off to China might seem like an invitation for competition, but Wells isn’t worried about it. He’s as busy as he wants to be and hopes more people will get involved the biochar-creating business.
New England Biochar LLC has four goals, he said. They are to: create the very best biochar; use the energy that comes off the system; eliminate the air and water pollution associated with traditional charcoal-making processes; and make it profitable so that lots of people will do it.
“I honestly believe that this is really good for the environment,” Wells said. “We are soaking up greenhouse gases better than any technology out there today.”